Manufacturing and Costing
Costing determines critical decision points such as which design is best but within budget, what quality of materials can be used, what efficiency of electrical components can be used. By implementing efficient cost management practice, we can set clear expectations, track progress, and respond with corrective action at a quick pace, maintain expected margin, increase ROI, avoid losing money on the project and generate data to track long-term cost trends
Some key areas that we focused on to ensure critical costing and management was achieved:
Project resource planning, this is the process of identifying the resources required to execute a project and take it to completion.
Cost estimation, this is the process of quantifying the costs associated with all the resources required to execute the project.
Cost budgeting, this is the process of allocating costs to a certain chunk of the project, such as individual tasks or modules, for a specific time period.
Cost control, this is the process of measuring cost variances from the baseline and taking appropriate action.
When the costing was executed, research through several different industrial websites and compare the costs but also the quality of each material, parts, and electrical components. In my findings, I soon came to realise that the smaller companies had more competitive prices whilst maintaining the same standard of quality, so these were the best sources for this project.
Costing Table
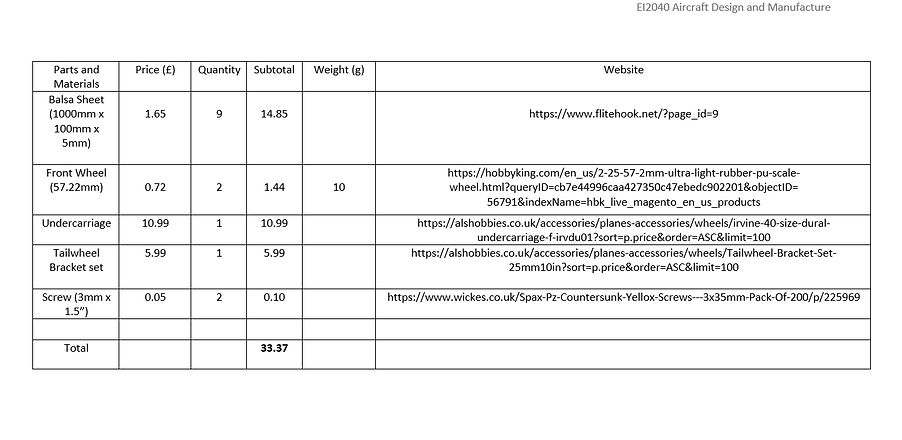
Material Selection
Carbon fibre, this is a lightweight polymer that is five times stronger than steel and twice as stiff. It has a high stress resistance and is durable in corrosive environments too. But its production costs are very high.
Polystyrene foam, the durability and strength of polystyrene foam makes it perfect for model-building of all kinds. It has good impact resistance, surface low water absorption, good anti-permeability, it is recyclable material. But it is highly flammable, the strength of the material is poor and is prone to cracking.
Plastics, they have a corrugated sheet structure that makes them extremely lightweight. Even more important for model airplane building, they are also waterproof, shockproof, and they resist corrosion. But they pollute our environment, pose a danger to wildlife, and they do not degrade quickly.
Balsa wood, it combines the two elements necessary to a successful flight: strength and lightness. Balsa wood is also easy to cut and carve with just a good, sharp hobby knife or razor saw, so no need for heavy power tools.
The primary material used in this project is balsa wood, this is the most ideal material for us to use as it is highly soft, lightweight, buoyant, and versatile. Its softness and flexibility make it perfect for model building, also it is the least expensive material from the previously mentioned options.
Manufacturing
We have access to several manufacturing machines in the location of manufacturing:
Milling machine, usually they are used to mill flat surfaces, but they can also be used to machine irregular surfaces. But you need to use a bit that is designed specifically for cutting softwood, this would be quite costly.
Lathe, it is a machine that is used primarily for shaping metal or wood. It works by rotating the workpiece around a stationary cutting tool. Mounting balsa wood into a lathe can be an issue due its soft nature.
Waterjet cutter, this is versatile applicable, cutting nearly any material, composites, plastics, metals, glass, stone or rock, ceramics, and rubber. For balsa wood it can cause damage, and possible discolouration of the surface.
Laser cutter, they work by directing a very powerful laser beam, at a precise focal length, onto a material which they either cut or etch.